1. ఎర్ర బట్టీ ఇటుక పడిపోవడం
కారణం:
(1) రోటరీ కిల్న్ స్కిన్ బాగా వేలాడదీయబడనప్పుడు.
(2) సిలిండర్ వేడెక్కి, వికృతంగా ఉంటుంది మరియు లోపలి గోడ అసమానంగా ఉంటుంది.
(3) కిల్న్ లైనింగ్ అధిక నాణ్యతతో లేదు లేదా సన్నగా అరిగిన తర్వాత షెడ్యూల్ ప్రకారం మార్చబడదు.
(4) రోటరీ కిల్న్ సిలిండర్ యొక్క మధ్య రేఖ నేరుగా ఉండదు; వీల్ బెల్ట్ మరియు ప్యాడ్ తీవ్రంగా అరిగిపోతాయి మరియు అంతరం చాలా పెద్దగా ఉన్నప్పుడు సిలిండర్ యొక్క రేడియల్ వైకల్యం పెరుగుతుంది.
ట్రబుల్షూటింగ్ పద్ధతి:
(1) బ్యాచింగ్ పని మరియు కాల్సినేషన్ ఆపరేషన్ను బలోపేతం చేయవచ్చు.
(2) ఫైరింగ్ జోన్ దగ్గర వీల్ బెల్ట్ మరియు ప్యాడ్ మధ్య అంతరాన్ని ఖచ్చితంగా నియంత్రించండి. అంతరం చాలా పెద్దగా ఉన్నప్పుడు, ప్యాడ్ను సకాలంలో మార్చాలి లేదా ప్యాడ్లతో సర్దుబాటు చేయాలి. ప్యాడ్ల మధ్య దీర్ఘకాలిక కదలిక వల్ల కలిగే అరిగిపోవడాన్ని నివారించడానికి మరియు తగ్గించడానికి, వీల్ బెల్ట్ మరియు ప్యాడ్ మధ్య లూబ్రికెంట్ జోడించాలి.
(3) పనిచేసేటప్పుడు కిల్న్ ఆపివేయబడిందని నిర్ధారించుకోండి మరియు అధిక వైకల్యంతో ఉన్న రోటరీ కిల్న్ యొక్క సిలిండర్ను సమయానికి మరమ్మతు చేయండి లేదా భర్తీ చేయండి;
(4) సిలిండర్ యొక్క మధ్య రేఖను క్రమం తప్పకుండా క్రమాంకనం చేయండి మరియు సహాయక చక్రం యొక్క స్థానాన్ని సర్దుబాటు చేయండి;
(5) అధిక-నాణ్యత గల బట్టీ లైనింగ్లను ఎంచుకోండి, ఇన్లే నాణ్యతను మెరుగుపరచండి, బట్టీ లైనింగ్ల వినియోగ చక్రాన్ని ఖచ్చితంగా నియంత్రించండి, ఇటుక మందాన్ని సమయానికి తనిఖీ చేయండి మరియు అరిగిపోయిన బట్టీ లైనింగ్లను సమయానికి భర్తీ చేయండి.
2. సహాయక చక్రం యొక్క షాఫ్ట్ విరిగిపోయింది
కారణాలు:
(1) సపోర్టింగ్ వీల్ మరియు షాఫ్ట్ మధ్య సరిపోలిక అసమంజసమైనది. సపోర్టింగ్ వీల్ మరియు షాఫ్ట్ మధ్య జోక్యం ఫిట్ సాధారణంగా షాఫ్ట్ వ్యాసంలో 0.6 నుండి 1/1000 వరకు ఉంటుంది, తద్వారా సపోర్టింగ్ వీల్ మరియు షాఫ్ట్ వదులుగా ఉండవని నిర్ధారించుకోవచ్చు. అయితే, ఈ జోక్యం ఫిట్ సపోర్టింగ్ వీల్ హోల్ చివరిలో షాఫ్ట్ కుంచించుకుపోతుంది, ఫలితంగా ఒత్తిడి ఏకాగ్రత ఏర్పడుతుంది. ఇక్కడ షాఫ్ట్ విరిగిపోతుందని ఊహించడం కష్టం కాదు మరియు ఇదే పరిస్థితి.
(2) అలసట పగులు. సహాయక చక్రం యొక్క సంక్లిష్ట శక్తి కారణంగా, సహాయక చక్రం మరియు షాఫ్ట్ను మొత్తంగా పరిగణించినట్లయితే, షాఫ్ట్ యొక్క వంపు ఒత్తిడి మరియు కోత ఒత్తిడి సహాయక చక్రం రంధ్రం చివర సంబంధిత భాగంలో అతిపెద్దవి. ఈ భాగం ప్రత్యామ్నాయ లోడ్ల చర్య కింద అలసటకు గురవుతుంది, కాబట్టి పగులు సహాయక చక్రం మరియు షాఫ్ట్ మధ్య ఉమ్మడి చివరలో కూడా సంభవించాలి.
(3) తయారీ లోపాలు రోలర్ షాఫ్ట్ను సాధారణంగా స్టీల్ కడ్డీలు లేదా రౌండ్ స్టీల్తో నకిలీ చేసి, యంత్రాలతో తయారు చేసి, వేడి చికిత్స చేయాలి. స్టీల్ కడ్డీలోని మలినాలు, క్రిమి చర్మాన్ని నకిలీ చేయడం మొదలైన లోపాలు మధ్యలో సంభవించి గుర్తించబడకపోతే మరియు వేడి చికిత్స సమయంలో మైక్రో క్రాక్లు కనిపిస్తాయి. ఈ లోపాలు షాఫ్ట్ యొక్క బేరింగ్ సామర్థ్యాన్ని పరిమితం చేయడమే కాకుండా, ఒత్తిడి సాంద్రతను కూడా కలిగిస్తాయి. ఒక మూలంగా, పగుళ్లు విస్తరించిన తర్వాత, పగులు అనివార్యం.
(4) ఉష్ణోగ్రత ఒత్తిడి లేదా సరికాని శక్తి రోటరీ బట్టీ యొక్క పెద్ద టైల్ను వేడి చేయడం ఒక సాధారణ లోపం. ఆపరేషన్ మరియు నిర్వహణ సరిగ్గా లేకపోతే, రోలర్ షాఫ్ట్పై ఉపరితల పగుళ్లు ఏర్పడటం సులభం. పెద్ద టైల్ వేడెక్కినప్పుడు, షాఫ్ట్ యొక్క ఉష్ణోగ్రత చాలా ఎక్కువగా ఉండాలి. ఈ సమయంలో, షాఫ్ట్ వేగంగా చల్లబడితే, షాఫ్ట్ యొక్క నెమ్మదిగా అంతర్గత శీతలీకరణ కారణంగా, వేగంగా కుంచించుకుపోతున్న షాఫ్ట్ ఉపరితలం పగుళ్ల ద్వారా భారీ సంకోచ ఒత్తిడిని మాత్రమే విడుదల చేయగలదు. ఈ సమయంలో, ఉపరితల పగుళ్లు ఒత్తిడి సాంద్రతను ఉత్పత్తి చేస్తాయి. ప్రత్యామ్నాయ ఒత్తిడి చర్యలో, పగుళ్లు చుట్టుకొలతగా విస్తరించి ఒక నిర్దిష్ట స్థాయికి చేరుకున్న తర్వాత, అది విరిగిపోతుంది. రోలర్పై అధిక శక్తికి కూడా ఇది వర్తిస్తుంది. ఉదాహరణకు, సరికాని సర్దుబాటు షాఫ్ట్ లేదా షాఫ్ట్ యొక్క ఒక నిర్దిష్ట విభాగంలో అధిక శక్తిని కలిగిస్తుంది, ఇది రోలర్ షాఫ్ట్ యొక్క పగుళ్లకు కారణం కావడం సులభం.
మినహాయింపు పద్ధతి:
(1) సపోర్టింగ్ వీల్ మరియు షాఫ్ట్ ఇన్క్లూజన్ ప్రాంతంలో వేర్వేరు జోక్య మొత్తాలను ఉపయోగిస్తారు. సపోర్టింగ్ వీల్ మరియు షాఫ్ట్ మధ్య జోక్య మొత్తం పెద్దగా ఉన్నందున, సపోర్టింగ్ వీల్ లోపలి రంధ్రం చివరను వేడిగా అమర్చిన తర్వాత, చల్లబరిచి బిగించిన తర్వాత షాఫ్ట్ ఈ ప్రదేశంలో కుంచించుకుపోతుంది మరియు ఒత్తిడి సాంద్రత చాలా ఎక్కువగా ఉంటుంది. అందువల్ల, డిజైన్, తయారీ మరియు ఇన్స్టాలేషన్ ప్రక్రియలో, నెక్కింగ్ సంభవించడాన్ని తగ్గించడానికి సపోర్టింగ్ వీల్ లోపలి రంధ్రం యొక్క రెండు చివరల జోక్య మొత్తం (సుమారు 100 మిమీ పరిధి) క్రమంగా లోపలి నుండి బయటికి తగ్గించబడుతుంది. నెక్కింగ్ దృగ్విషయాన్ని నివారించడానికి లేదా తగ్గించడానికి తగ్గింపు మొత్తాన్ని క్రమంగా మధ్య జోక్య మొత్తంలో మూడింట ఒక వంతు నుండి సగం వరకు తగ్గించవచ్చు.
(2) లోపాలను తొలగించడానికి సమగ్ర దోష గుర్తింపు. లోపాలు షాఫ్ట్ యొక్క బేరింగ్ సామర్థ్యాన్ని తగ్గిస్తాయి మరియు ఒత్తిడి సాంద్రతకు కారణమవుతాయి, ఇది తరచుగా పగులు ప్రమాదాలకు కారణమవుతుంది. హాని చాలా గొప్పది మరియు దీనిని తీవ్రంగా పరిగణించాలి. సపోర్టింగ్ వీల్ షాఫ్ట్ కోసం, లోపాలను ముందుగానే కనుగొనాలి. ఉదాహరణకు, ప్రాసెస్ చేయడానికి ముందు, మెటీరియల్ ఎంపికను తనిఖీ చేయాలి మరియు ఎటువంటి సమస్య లేని పదార్థాలను ఎంచుకోవాలి; లోపాలను తొలగించడానికి, షాఫ్ట్ యొక్క అంతర్గత నాణ్యతను నిర్ధారించడానికి మరియు అదే సమయంలో షాఫ్ట్ యొక్క ప్రాసెసింగ్ ఖచ్చితత్వాన్ని నిర్ధారించడానికి మరియు క్రాక్ మూలాలు మరియు ఒత్తిడి సాంద్రత మూలాలను తొలగించడానికి ప్రాసెసింగ్ సమయంలో దోష గుర్తింపును కూడా నిర్వహించాలి.
(3) అదనపు లోడ్లను తగ్గించడానికి బట్టీని సహేతుకంగా సర్దుబాటు చేయడం. రోలర్ల ద్వారా బట్టీ యొక్క మొత్తం బరువును బహుళ రోలర్ షాఫ్ట్లు తట్టుకుంటాయి. లోడ్ చాలా పెద్దది. సంస్థాపన లేదా నిర్వహణ సర్దుబాటు సరిగ్గా లేకపోతే, అసాధారణ లోడ్ ఏర్పడుతుంది. బట్టీ యొక్క మధ్య రేఖ నుండి దూరం అస్థిరంగా ఉన్నప్పుడు, ఒక నిర్దిష్ట రోలర్ అధిక శక్తికి లోనవుతుంది; రోలర్ యొక్క అక్షం బట్టీ యొక్క మధ్య రేఖకు సమాంతరంగా లేనప్పుడు, షాఫ్ట్ యొక్క ఒక వైపున ఉన్న శక్తి పెరుగుతుంది. సరికాని అధిక శక్తి పెద్ద బేరింగ్ వేడెక్కడానికి కారణమవుతుంది మరియు షాఫ్ట్ యొక్క ఒక నిర్దిష్ట బిందువు వద్ద పెద్ద ఒత్తిడి కారణంగా షాఫ్ట్కు కూడా నష్టం కలిగిస్తుంది. అందువల్ల, అదనపు లోడ్లను నివారించడానికి లేదా తగ్గించడానికి మరియు బట్టీని తేలికగా నడిపించడానికి బట్టీ యొక్క నిర్వహణ మరియు సర్దుబాటును తీవ్రంగా పరిగణించాలి. నిర్వహణ ప్రక్రియలో, షాఫ్ట్పై అగ్నిని ప్రారంభించడం మరియు వెల్డింగ్ను నివారించండి మరియు షాఫ్ట్కు నష్టాన్ని తగ్గించడానికి గ్రైండింగ్ వీల్తో షాఫ్ట్ను గ్రౌండింగ్ చేయడాన్ని నివారించండి.
(4) ఆపరేషన్ సమయంలో వేడి షాఫ్ట్ను వేగంగా చల్లబరచవద్దు. కిల్న్ ఆపరేషన్ సమయంలో, పెద్ద బేరింగ్ కొన్ని కారణాల వల్ల వేడిని కలిగిస్తుంది. ఈ సమయంలో, ఉత్పత్తి నష్టాలను తగ్గించడానికి, కొన్ని యూనిట్లు తరచుగా వేగవంతమైన శీతలీకరణను అవలంబిస్తాయి, ఇది షాఫ్ట్ ఉపరితలంపై మైక్రో క్రాక్లను కలిగించడం సులభం, కాబట్టి వేగవంతమైన శీతలీకరణను నివారించడానికి నెమ్మదిగా శీతలీకరణను అవలంబించాలి.
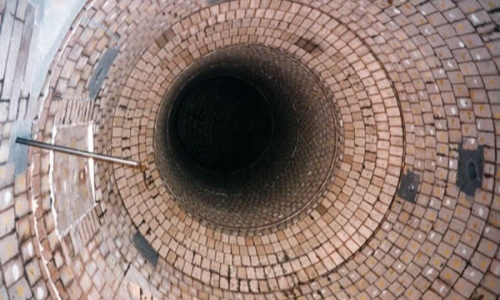
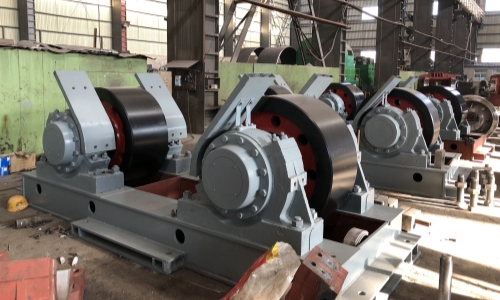
పోస్ట్ సమయం: మే-12-2025